You are here: Home > Rental Equipment > Forklift & Material Handling Rental | ||||||||||
Forklift Rental Telescopic 62' 8000lbs. (Lull 1044C-54 w/ Tower) F054Safety Information
Introduction
Every year nearly 100 workers are killed and 20,000 are seriously injured in forklift mishaps. According to the National Traumatic Occupational Fatalities (NTOF) Surveillance System, 1,530 workers died from forklift related accidents between 1980 and 2001. The top four types of incidents as a percent of the total forklift related deaths are: Whenever you see either of these two symbols in these safety and operating instructions, it means that failure to follow the instructions can result in serious injury or death. Types of Forklifts A forklift is a type of "powered industrial truck." Like other powered industrial trucks, its purpose is to move, carry, push, pull, and lift a material load then stack it or place it in a storage rack (tier). Forklifts come in many sizes and capacities. They can be powered by batteries, propane, gasoline or diesel fuel. Some are designed to be used in a hazardous location or atmosphere where an ordinary forklift might cause a fire or explosion. Powered industrial trucks are classified into seven types based on their characteristics. The seven types of forklifts are:
Types of Forklifts. Safely Using a Forklift Failure to check that the forklift is operating properly can lead to an accident Pre-use inspection The forklift must be checked for defects daily — usually by the operator before beginning a shift. Even if you operate a forklift safely, a defect can cause or contribute to a serious accident. Some things to look for are:
Any defects that would affect safety must be corrected before the forklift is returned to service. Appendix A is a sample operator pre-use inspection checklist. Surface Condition The surface a forklift operates on can cause serious safety problems. Loose objects, bumps, or depressions can cause you to lose control of steering, bring you to a sudden unplanned stop or cause you to drop your load. A soft dirt surface can cause a wheel to sink and destabilize an elevated load and the forklift. Any surface a forklift drives on must be able to support the forklift and its load with a safety factor of four. If a 7,000 pound forklift is carrying a 3,000 pound load then the floor must be able to support 40,000 pounds. Remember that nearly the full weight of the load plus a part of the weight of the forklift may be centered near a single wheel. Wet, oily or icy surfaces should be avoided. Clean them up as soon as possible. Traveling The basic rule for traveling is that you maintain control of your forklift at all times. Other rules include:
Driving onto trucks, trailers, and railroad cars Failure to secure the truck or trailer with blocks can cause the trailer to move resulting in the forklift falling between the trailer and the dock. Forklifts are often driven onto trucks, trailers, or railroad cars over a dock board (also known as a bridge plate) at loading docks. If the truck, trailer or car is not secured to the dock or otherwise chocked, it can move over time. The dock board can then fall between the trailer and the dock as the forklift crosses it. You can secure wheel chocks with chain at each loading dock bay and tell truck drivers that they must place them in front of the rear wheels. Another way of securing the trailer is to use a vehicle restraint system mounted to the dock that clamps onto a bar below the trailer as it backs into place. This system will signal when the restraint is engaged or if there is a problem. The pavement at some loading docks slopes downhill toward the loading dock. This is not a substitute for chocking wheels. Sometimes a trailer is left at a loading dock without the tractor attached. Use trailer jacks to prevent the trailer from up-ending when a forklift drives to the front of the trailer to load or unload. An unsecured dock plate can move over time resulting in a sudden stop of the forklift and loss of the load as the wheels lodge in the space between the dock and the truck bed. A portable dock board must be secured in place to prevent it from moving. Some boards have pins that are inserted into the sides and project below the board. This prevents the board from moving toward the dock or toward the trailer. To prevent crushed fingers and make for safe handling, a portable dock board must also have handholds or lugs that allow the forklift to pick it up. Keep a safe distance from the edge of a loading dock or a ramp. The edge must be painted yellow or with alternating yellow and black diagonal stripes to warn of both the fall hazard and the potential to be crushed by a trailer backing into the dock. Some loading docks have a bull rail that prevents a wheel from slipping off the sides of ramps or edges of the dock where a forklift would not have to cross to enter a trailer. Any part of the dock edge that is four feet or more above the adjacent surface must have a standard guardrail. Removable rails (such as chain rails) and posts can be used at the place where trucks or trailers will be loaded. Loading and unloading the forklift Check the load before you pick it up.
When you place the load at its destination:
Leaving a forklift unattended A forklift is considered to be unattended when it is not in view of the operator or if it is in view, the operator is 25 feet or more away. If you leave a forklift unattended, lower the forks to the ground. Set the controls to neutral, turn off the power, and set the brakes. If the forklift is on an incline, block the wheels. If you dismount a forklift and stay within 25 feet, you must at least lower the forks to the ground, set the controls to neutral and set the brakes. Lifting or lowering a person on forks or a pallet can result in a fall injury or fingers caught in moving parts of the mast. Lifting and lowering people Never allow anyone to be lifted while standing on the forks or on a pallet lifted by the forks! If you want to use a forklift to raise an employee to an elevated position, use a platform or structure specifically built for this purpose that meets these conditions:
Fueling/charging These practices are designed to prevent explosion of flammable vapors due to spark or collision with unprotected fuel tanks. When refueling or charging batteries, observe the following precautions:
Liquid Petroleum Gas (LPG) forklifts
Gasoline or diesel forklifts
Carbon monoxide hazard Internal combustion engines produce carbon monoxide. This gas can rapidly build up in any indoor area. People can be overcome without even realizing they are being exposed. Confusion, headache, dizziness, fatigue, and weakness may set in too quickly for victims to save themselves. Carbon monoxide poisoning can cause permanent brain damage, including changes in personality and memory. Once inhaled, carbon monoxide decreases the ability of the blood to carry oxygen to the brain and other vital organs. Even low levels of carbon monoxide can set off chest pains and heart attacks in people with coronary artery disease. Gasoline powered forklifts should not be used indoors. Propane forklifts also produce carbon monoxide and must be regularly inspected and maintained. If you are concerned about the exposure level in an enclosed area where a forklift operates, contact a qualified industrial hygienist to make measurements and recommendations to improve ventilation. Operating a forklift in an environment where chemicals or other substances are present can be hazardous. Use only forklifts that are acceptable for operations under those conditions. To select the appropriate forklift, you must know the type of location (Class), the name of the chemical or substance and how likely it is that the hazardous condition would be present (Division). Terms
Out of Service and Required Check Intervals Some employers keep records of these daily checks. If a forklift is found unsafe then it must be removed from service until repaired by an authorized person. In addition, the forklift owner’s manual will have routine checks and preventive maintenance tasks that must be done by a skilled maintenance person to keep the forklift in safe operating condition. Keep a record of this maintenance as well as any repairs that are made. Do not alter or eliminate any forklift parts or add any accessories such as additional counterweights or lifting attachments unless approved by the manufacturer in writing. Make any necessary changes to the load capacity plate and operating instructions. |
We know your business success depends on reliable quality equipment and parts to continue being a leader in your industry. When you want Genuine Lull original equipment parts, accessories and equipment you can always depend on Discount-Equipment.com to come through with the genuine o.e.m. products you need as quickly and inexpensive as possible. Our sales staff combined experience consists of over 90 years in the construction parts and equipment industry. We have over 1 million items online, if you are having trouble finding your item, we also have the resources to help you find what you need, our industry leading web site includes thousands of parts and service manuals available to look up your items. If you don't find what you are looking for please fill out our parts request form here.
Search
Shopping Cart
Your cart is empty |
Manufacturer/Brand
Equipment Type
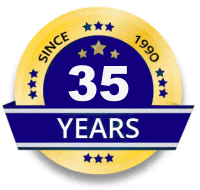
Edit this page